Photonics HandbookLasers
Semiconductor Lasers: An Overview of Commercial Devices
Within only a few decades, the semiconductor laser diode has evolved into a family of robust, reliable devices, with individual conversion efficiencies of better than 60 percent, continuous output powers of several kilowatts, modulation rates of several tens of gigahertz, and wavelengths from 0.4 to beyond 2 µm. This article discusses the structures and characteristics of the most common commercial varieties.
JDSU
Laser diodes vary widely in their wavelengths, powers, spectra and beam quality. Yet they share two fundamental components with all other lasers: an optical amplifier and a resonator that confines and recirculates light through the amplifying element.
In the diode laser, the amplifying element is a forward-biased PN junction formed in a direct-bandgap semiconductor. Optical gain is provided by the recombination of electrons and holes in the PN junction. When forward biased, electrons are injected from the N side while holes are injected from the P side; both electrons and holes are confined within a lower bandgap region where they can recombine either spontaneously or via stimulated emission when excited by an existing photon. (They also can recombine nonradiatively, a parasitic process that degrades performance.)
Operating voltage is determined by the bandgap of emitted light plus a linear factor caused by series resistance; for 1-µm radiation, the operating voltage is around 2 V. Diode lasers can be extremely efficient. For example, recent progress on the “wallplug” efficiency (i.e., conversion of electrical input power to optical output power) of diode lasers operating in the 940-nm wavelength range is approaching 70 percent.
The resonator continuously recirculates light and is responsible for the high level of coherence, both spatial (focusable to a very small spot) and spectral (consisting of a narrow range of frequencies). In most cases, the resonator includes a waveguide that confines the light in two dimensions, causing it to travel back and forth along a predominantly linear path.
The resonator is bounded by mirrors that usually are formed by cleaving facets at each end of the waveguide. A resonator composed of two plane-parallel mirrors is called a Fabry-Perot resonator; most laser diodes are of that type.
The mirror facets are coated with a dielectric film to increase or decrease reflectivity and to improve resistance to damage from the extremely high power densities — up to 100 MW/cm2. Generally, one facet is coated with a high-reflectivity (99 percent) coating, while the one from which the output is taken has a reflectivity from 1 to 10 percent. The vast majority of diode lasers emit with polarization in the plane of the chip; exceptions include some visible lasers.
The electrically pumped PN junction is qualitatively the same for all semiconductor lasers — differing only in the choices of materials, dopants and layer thickness, which affect the wavelength, efficiency, power-handling capability and so forth.
Identical or similar epitaxial structures also are used in several nonlaser devices: semiconductor optical amplifiers used in fiber optic transmissions systems; and edge-emitting LEDs, called superluminescent diodes, which emit an incoherent, broadband radiation that is used in various specialized sensors and communications systems.
Materials and wavelengths
In principle, a diode laser can be produced from any direct-bandgap semiconductor. However, efficient, electrically injected lasers require precisely doped layered structures of varying alloys that are all lattice-matched to one another and to a substrate. These requirements place some limitations on the available materials.
Commercial semiconductor lasers are all III-V compounds — alloys of Group III and Group V elements in the periodic table. There are two major commercial families of semiconductor lasers — those grown on GaAs substrates and those grown on InP substrates.
GaAs-based lasers are formed from alloys of Ga, Al, In and As, P, grown in compositions lattice-matched to GaAs. They can emit at any wavelength from about 630 to about 1100 nm, the most common commercial ones being 635, 650, 680 and 780 nm, which are used in optical storage and displays; 785, 808, 830, 920 and 940 nm, which are used for various pumping and printing applications; and 980 nm, which is used for pumping fiber amplifiers in telecommunications.
InP-based lasers are formed from alloys of the same constituents, Ga, Al, In and As, P, but in compositions that are lattice-matched to InP. They range from about 1100 to 2000 nm, but by far the most common are emitters at 1300, 1480 and 1550 nm, which are used in fiber optic communications.
Longer wavelengths — out to about 10 μm — are possible by incorporating other materials (e.g., Sb) into the alloy and/or by using different substrates. Shorter wavelengths, down to about 400 nm, have been demonstrated by growing GaN and related alloys, and commercial lasers in the near-UV are under development.
Single-spatial-mode lasers
The simplest and most common laser diode is the single-spatial-mode (also called single transverse mode) laser. Single spatial mode implies that the beam can be focused to a diffraction-limited spot. (This is not to be confused with the term single longitudinal mode, or single frequency, which refers to the optical spectrum.) The term single mode can be, and often is used to refer to both types of laser.
Figure 1 shows a typical single-spatial-mode laser with a relatively narrow waveguide bounded by the cleaved facets. The narrow waveguide, which may be formed by a ridge or by a buried index step, supports only a single optical mode. This limits it to a width of 2 to 5 μm, depending on the details of the waveguide structure. The light emitted by a single-mode laser is, at the facet, typically 1 μm high by 3 to 4 μm wide. Upon leaving the facet, the light diffracts, creating a diverging beam that is typically 20° to 30° (FWHM) in the vertical direction (perpendicular to the plane of the junction, also called the fast axis) and 5° to 10° in the horizontal direction (in the plane of the junction, also called the slow axis).
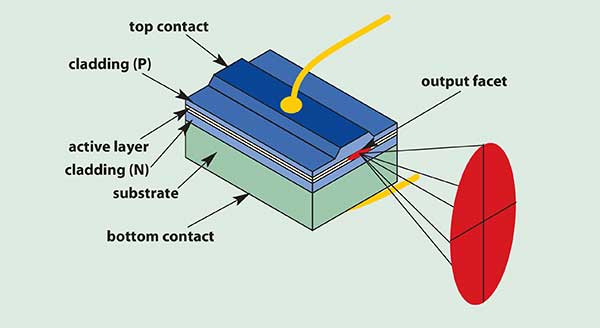
Figure 1. A single-transverse-mode laser diode exhibits the basic laser configuration.
To the optical designer, the beam appears to be an ideal point source. It is, however, anamorphic because the divergences in the two perpendicular directions are different. In addition, many single-spatial-mode lasers are slightly astigmatic, with values ranging from a fraction of a micron up to several tens of microns, depending on the specific laser structure. Both anamorphism and astigmatism can be corrected with relatively simple optics.
Single-spatial-mode lasers are used wherever a diffraction-limited spot is required, such as optical data storage (the largest unit volume application for all laser diodes), thermal and xerographic printing, as pumps and transmission sources in single-mode optical fiber communications and in the ubiquitous laser pointer. Because of the narrow waveguide imposed by the requirement of single-mode operation, the local power density and thermal dissipation are significant and limit the maximum average power to somewhere below 1000 mW. This power can be raised by more sophisticated laser structures.
The Fabry-Perot resonator in a single-spatial-mode laser diode can support multiple longitudinal modes — wavelengths separated by about 1 Å. While many Fabry-Perot diodes can at times run in a single longitudinal mode, they are susceptible to unpredictable mode hops, and either modulation or fairly low levels of feedback can destabilize the laser, causing it to run in multiple longitudinal modes.
Multimode lasers
The limit on total output power from a single-mode laser comes from considerations of power density within the narrow waveguide. Lower power density and higher powers can be obtained simply by making the laser structure wider, raising the width from 3 or 4 µm up to 50, 100 or 200 µm. The wider lasers can operate at much higher powers — up to 2 W is typical from a 100-µm aperture though higher powers are becoming commercially available (4 to 6 W) — at the expense of losing spatial coherence. These lasers are called broad-area, or multimode lasers.
They cannot be focused to a diffraction-limited spot or efficiently coupled into a single-mode fiber. Note, too, that although the facet may be 30 times wider, the maximum power of a multimode laser is less than 30 times higher than that of a single-mode laser. Maximum power typically increases sublinearly with laser width.
Nevertheless, many applications such as pumping solid-state lasers and external-drum thermal printing do not require a diffraction-limited spot, and multimode lasers, with their high average powers, are the laser of choice in such applications. Total electrical-to-optical conversion efficiencies can exceed 60 percent in such devices.
Bars and stacks
If the application requires powers in excess of a few watts, the output of multiple laser emitters must be combined. The next level up in the hierarchy of laser power is the laser bar, which is an array of 10 to 50 side-by-side multimode lasers integrated into a single chip. Standard bar dimensions are either 1.0 cm wide by 500 to 2000 µm long. A single bar can emit 20 to 60 W of average power when operated continuous wave (CW), or over 100 W of peak power when operated in a pulsed mode in which duty cycles can run up to 20 percent.
The most common application for bars is pumping solid-state lasers; commercially available wavelengths, therefore, are those required by various laser crystals. The most common is 808 nm, used for pumping Nd:YAG; others include 785, 792, 915 and 940 nm.
Still higher powers are attainable by mounting bars into stacks, in which all of the bars are driven in series (Figure 2). The bar stack offers high power densities, while the series connection provides a more tractable impedance to the laser drive electronics. A 40-W bar will require 40 to 50 A of drive current at about 2-V drive voltage; multibar stacks increase the drive voltage but have the same current requirements as a single bar.
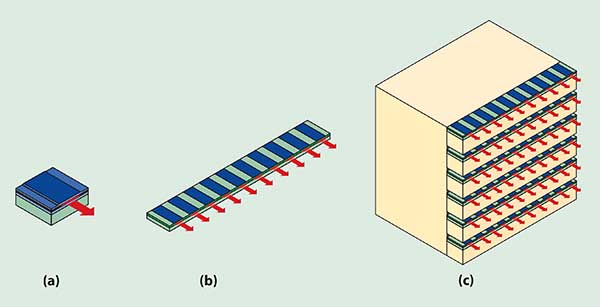
Figure 2. Diode powers (a) can be increased by combining them into bars (b), and stacks of bars (c).
When stacks are used to pump slab lasers, they are not lensed, but simply positioned directly next to the laser crystal. However, for some applications — end-pumping, laser beacons/illuminators and the growing field of direct diode laser materials processing — a stack will be lensed by positioning an array of cylindrical lenses (monolithic or individual, depending on the required brightness) in front of the array of laser bars. At powers above a few tens of watts, the power dissipation exceeds the power handling capability of passive or thermoelectric coolers, and large laser stacks are nearly always water-cooled.
Single-mode DFB
The ever-growing capacity in fiber optic transmissions systems requires a laser source with low noise and extremely narrow frequency spectrum. This need is met by the distributed-feedback (DFB) laser (Figure 3), which differs from all of the lasers discussed thus far. Instead of relying on mirrors to provide feedback within the laser resonator, it uses a grating — a corrugated structure — embedded within the laser structure in close proximity to the waveguide. Each ripple in the grating provides a minute amount of feedback. The device operates only at the single frequency for which the feedback from the ripples add up in phase. Thus, distributed-feedback lasers operate in a single frequency and remain single frequency under modulation and variations in drive current or operating temperature. Single-frequency operation also eliminates a major source of noise in semiconductor lasers, called partition noise, that results from competition between longitudinal modes in multifrequency lasers, and therefore they tend to be among the quietest of diode lasers, with relative intensity noise levels of –150 dB/Hz.
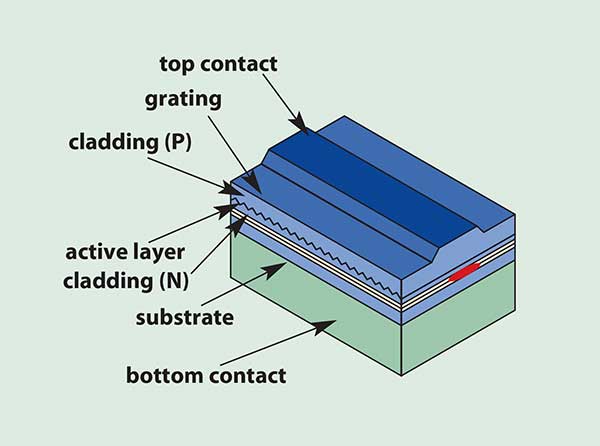
Figure 3. The distributed-feedback laser employs a grating, rather than mirrors.
By far the largest application of distributed-feedback lasers is in fiber optic transmission systems. The first commercial devices were at 1.3 µm; now most are around 1.55 µm to match the low-loss window of silica optical fiber and the gain bandwidth of erbium-doped fiber amplifiers. Commercially, most are sold fiber-coupled; typical output powers range from 1 to 35 mW in the fiber.
A small number are used for various interferometric or spectroscopic applications. In such applications, the desired wavelength is set by a particular atomic or molecular absorption line, or in the case of interferometry, for compatibility with existing gas lasers (e.g., HeNe). Distributed-feedback lasers have been demonstrated for such applications at wavelengths from 633 to 2000 nm and beyond.
Uncommon laser structures
Although the majority of lasers sold today fall into one of the above categories, several other types have been demonstrated and are sold commercially.
The most novel is the vertical-cavity surface-emitting laser, or VCSEL. Unlike the other lasers presented above, in which the light propagates in the plane of the semiconductor wafer, in the VCSEL, light travels perpendicularly to the wafer and is emitted from the surface (Figure 4). The mirrors are typically provided by growing multilayer dielectric stacks above and below the quantum well active layer; lateral confinement is provided either by gain-guiding or, in newer devices, by an annular ring of oxidized AlAs.
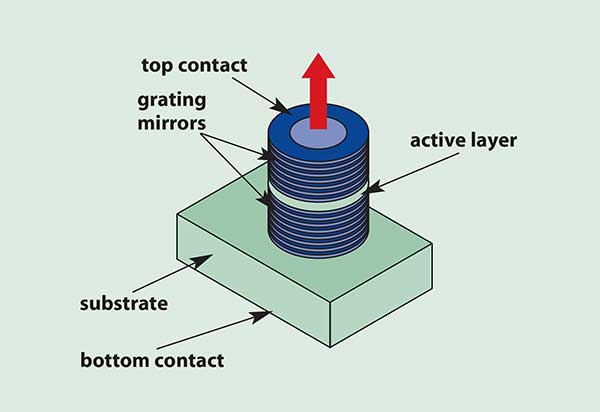
Figure 4. The VCSEL emits in a vertical rather than a horizontal plane.
VCSELs are much more difficult epitaxial structures to grow than edge-emitting lasers; the multilayer stacks must have reflectivities as high as 99.8 percent and the layer thicknesses must be precisely controlled to ensure that the resonator frequency falls within the gain bandwidth of the quantum well. However, because they have no cleaved facets, they can be completely fabricated and tested at the wafer level, so their processing subsequent to growth is considerably simpler. In addition, their low power requirements — thresholds can be well below 1 mA — and their low-divergence, nearly circular beam profile make them well suited to coupling to optical fibers. Because of these properties, VCSELs have found a solid application in low-cost, multimode fiber links, particularly in linear and two-dimensional arrays.
DBRs and tunable DFBs
The presence of a buried grating is what makes a distributed-feedback laser operate in a single frequency. More complicated laser structures combine gratings with grating-free waveguide regions and two or more contacts to give monolithic tunable lasers. The distributed Bragg reflector (DBR) laser replaces one of the facets of a Fabry-Perot laser with a grating similar to that of the DFB. It provides higher CW powers than an equivalent DFB laser, at the cost of introducing mode hops with drive current. Addition of a second contact to the grating region gives wideband tunability. DBR lasers and their variants are used for various spectroscopic and instrumentation applications.
/Buyers_Guide/Lumentum_Operations_LLC/c7335