Optical Components: Finding Your Way Through the Maze
Optical components fall into two basic groups: transmissives and reflectives. Transmissives include lenses, filters, windows, optical flats, prisms, polarizers, beamsplitters, wave plates, and fiber optics; reflectives include mirrors and retroreflectors. The performance of all may be enhanced with certain substrates and thin film coatings.
CVI Melles Griot
Lenses come in a variety of shapes, sizes and materials. They can be made of a single piece of glass or have multiple elements; their surfaces can be spherical, aspheric or cylindrical; they can be made from any of several hundred common glasses or from more complex materials such as fused silica or calcium fluoride.
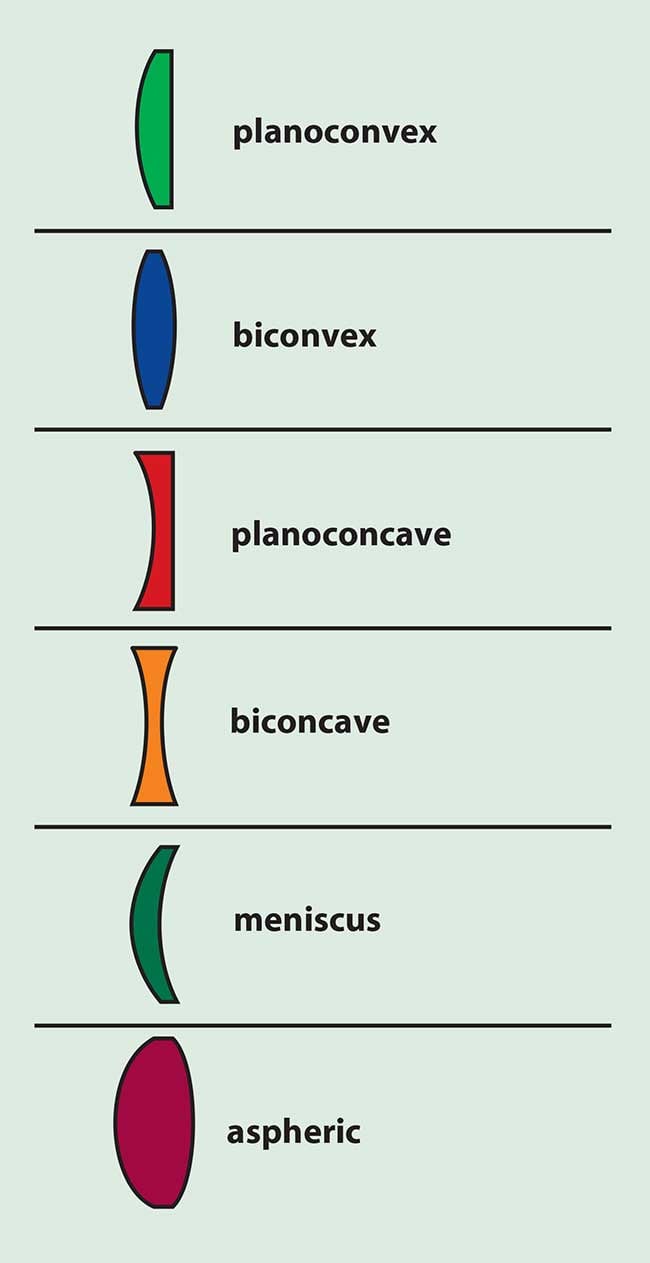
Figure 1. Singlet lenses come in a variety of basic shapes.
Singlets come in several basic shapes: planoconvex, biconvex, planoconcave, biconcave, meniscus (concave/convex), and aspheric (Figure 1). The shape that minimizes spherical aberration in an optical system is called best-form and is dependent upon the index of refraction of the lens material and the ratio of the object and image distances (the conjugate ratio) in the system. At infinite conjugate, an off-the-shelf planoconvex glass singlet with the convex side facing the infinite conjugate will perform nearly as well as a customized best-form lens, but at a much lower cost.
For imaging at unit magnification (object distance = image distance), a symmetric biconvex lens not only is best-form, but coma, distortion and lateral chromatic aberration cancel each other out. This is true regardless of material index or wavelength and explains the utility of symmetric convex lenses, as well as symmetrical optical systems in general.
Off-the-shelf singlets are typically made of BK7, because this material is easily manufactured, plentiful and transmissive from approximately 350 nm to the near-IR (Figure 2). Fused silica, though more expensive than BK7, also is used in off-the-shelf optics because of its greater UV and IR transmission as well as its temperature stability, hardness and resistance to scratching.
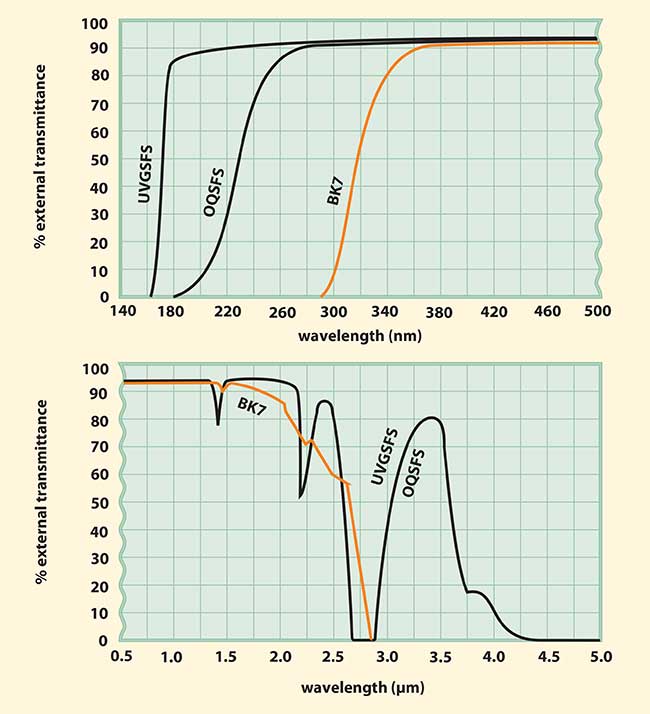
Figure 2. Comparison of external transmittances for UV-grade synthetic fused silica (UVGSFS), optical quality synthetic fused silica (OQSFS) and BK7, all 10 mm in thickness.
Achromatic doublets, also called achromats, are closely spaced, often cemented combinations of positive and negative elements with differing indices of refraction, which allow two distinct and well-separated wavelengths to be corrected for chromatic aberration. Achromats are nearly free from spherical aberration and coma, an advantage over simple singlets.
Symmetric lens system designs can improve imaging performance, especially for one-to-one, on-axis applications. The simplest example system is a symmetric biconvex lens. A symmetric system that offers significantly improved performance comprises a pair of identical planoconvex lenses with their curvatures facing each other. Using a pair of identical achromats will increase resolution even further (Figure 3).
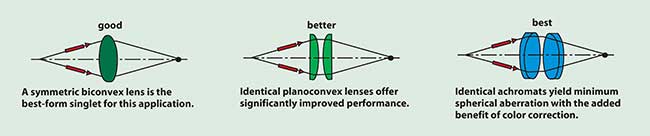
Figure 3. Three symmetric lens systems commonly used in imaging applications. Imaging systems requiring a low f/# or a wide field of view require more complex designs.
Imaging applications with a wide field of view or requiring a low f/# will need more complex optical designs including at least three elements, all varying in shape, thickness and material.
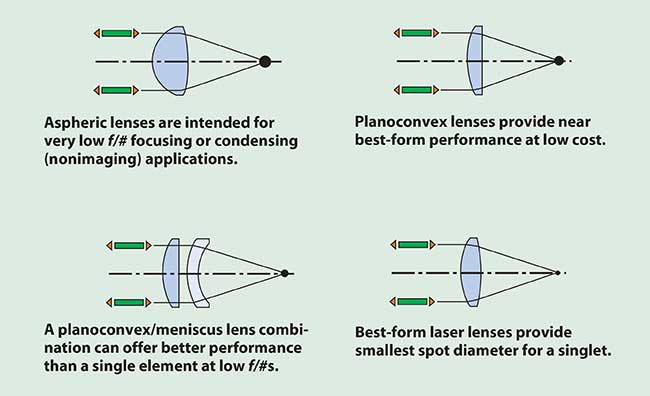
Figure 4. There are several ways to focus collimated light to a small on-axis spot. Applications, cost and requirements determine which configuration to use.
A single, symmetric, biconvex lens will focus collimated light to a small on-axis spot; however, because it is closer to best-form, a planoconvex lens is a better choice. The ideal singlet focusing lens is a nonsymmetric, biconvex, best-form lens specifically designed for the wavelength of interest with both surface curvatures optimized for minimal aberration (Figure 4). The best choice for focusing on-axis is an achromatic doublet, which provides both color correction and minimum spherical aberration and results in a smaller focused spot size than any of the singlets. For greater light-gathering power, the f/# of an achromatic focusing lens can be effectively decreased without degrading performance by combining it with a meniscus lens that is designed to be aplanatic (i.e., introducing no additional spherical aberration or coma), as shown in Figure 5.
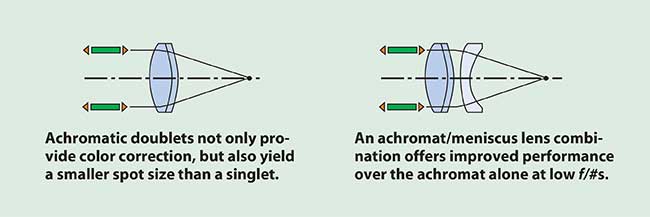
Figure 5. Achromatic doublet lenses are color corrected and nearly free from spherical aberration and coma.
Filters
Filters alter the characteristics of a beam of light either by changing the overall intensity of the beam without affecting its spectral content (e.g., neutral density filters) or by changing or separating the spectral content of the beam through wavelength-selective absorption or reflection (e.g., high-pass, low-pass, edge, dichroic and interference filters).
Two commonly used filter materials are thin metallic films and colored glass. The reflection properties of metallic films such as Inconel, chromium and nickel are relatively insensitive to wavelength. On the other hand, the absorption characteristics of colored glass can vary by as much as several orders of magnitude over a small wavelength range.
Neutral density filters attenuate, split or combine beams in a range of irradiance ratios with little dependence on wavelength. Metallic neutral density filters have an Inconel coating deposited on a glass plate. The coating thickness determines the amount of transmission. Absorptive neutral density filters are constructed from colored glass, whose thickness is varied to control its transmission. Neutral density filters are specified in terms of optical density (D), which is defined as the base 10 logarithm of the reciprocal of transmittance (T):

The optical densities of neutral density filters used in combination are additive if multiple reflections between filters do not occur in the direction of interest. Filter combinations can provide values of transmittance or density not otherwise available.
Interference filters — multilayer thin-film components that isolate and identify specific regions by reflecting the longer wavelengths and absorbing the shorter ones — provide a simple, economical way to isolate a specific wavelength or wavelength range. The transmitted wavelength range or passband of these filters can be designed to be less than 1 nm or greater than 100 nm, as defined by the full width half maximum of the transmission curve. The passband of most standard interference filters, however, ranges from 10 to 80 nm.
Windows and flats
Windows pass radiation from one environment to another without allowing elements of either to mix. The environments may vary widely in temperature, pressure, chemical composition, phase or cleanliness. The criteria used to select the appropriate window include wavelength transmission, scattering, wavefront distortion and resistance to certain elements.
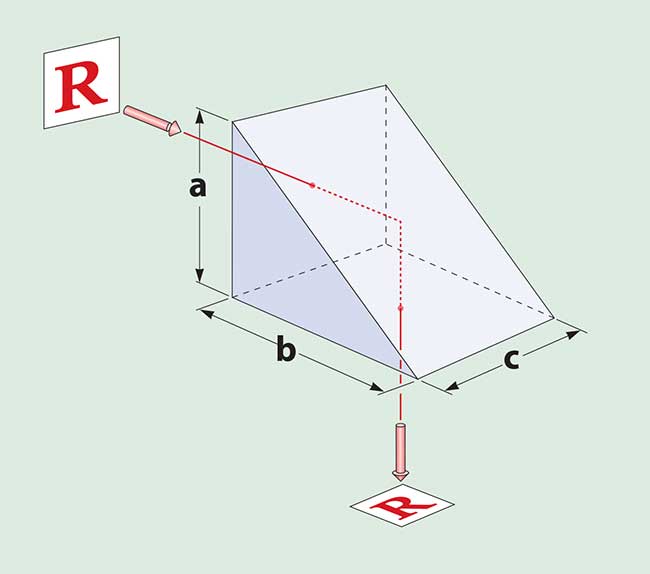
Figure 6. A right-angle prism deviates the beam by 90°.
Optical flats are references that are used to test and evaluate surfaces of other optical elements. The flat is placed on the surface to be evaluated, and an interference pattern is formed in the gap between the surfaces. The shape and curvature of the interference fringes indicate the shape of the surface being tested. The fringe pattern is usually more easily seen through the flat than the object under test. Therefore, it is advantageous to have an antireflection coating on the viewer's side surface (the surface that does not touch the object being evaluated).
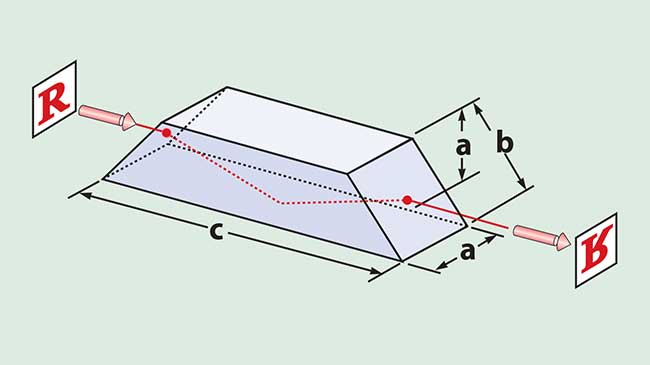
Figure 7. The dove prism is used as an image rotator. As the prism is rotated, the image rotates at twice the angular rate of the prism.
Prisms
Prisms are blocks of optical material with flat, polished sides arranged at precisely controlled angles. Because small errors can inhibit proper operation, angle specifications are critical. Prisms deflect or deviate light, invert or rotate an image, disperse light into component wavelengths, and separate polarization states. There are many kinds of prisms, many of which make use of the property of total internal reflection (TIR). Light incident upon an air/glass boundary at angles greater than the critical angle (approximately 42° for visible light and BK7 glass) is totally reflected.
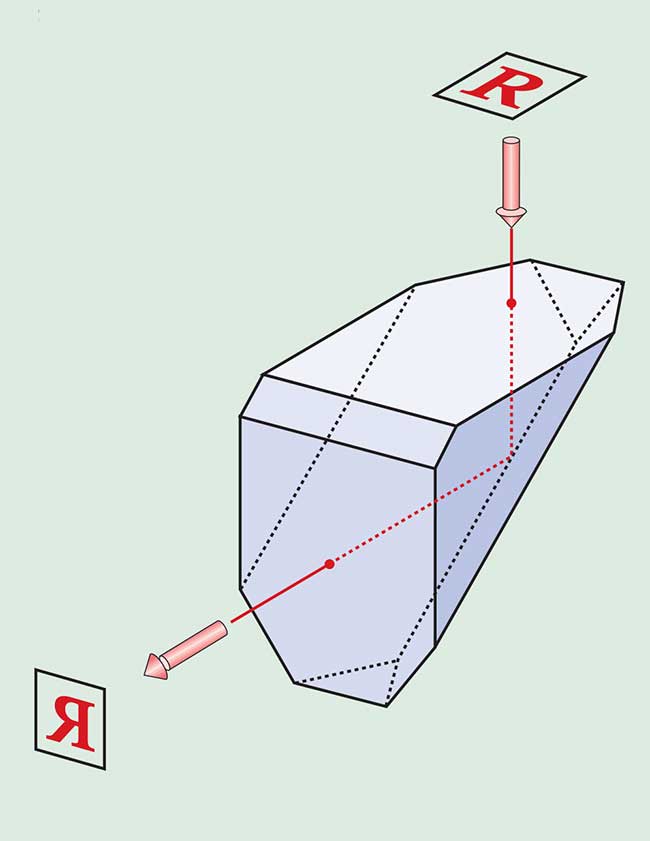
Figure 8. The roof, or Amici, prism is a right-angle prism whose hypotenuse has been replaced with a right-angle roof. This deflects the beam by 90° and rotates the image 180° about the optical axis.
The common right-angle prism is used to bend light through 90° (Figure 6). The dove prism is used as an image rotator (Figure 7); the roof (or Amici) prism both deflects light by 90° and inverts the image (Figure 8); the penta prism deflects light by 90° but does not invert or reverse the image (Figure 9); the equilateral dispersing prism is used for wavelength separation (Figure 10); and the wedge prism is used for beam steering (Figure 11). Prisms made of birefringent materials like calcite are used to separate polarization states.
Optical materials that possess both desirable transmission characteristics and mechanical properties become increasingly scarce with shorter wavelength. UV-grade fused silica performs well at wavelengths down to 190 nm, but at shorter wavelengths, calcium fluoride (CaF2) and magnesium fluoride (MgF2) are the only choices.
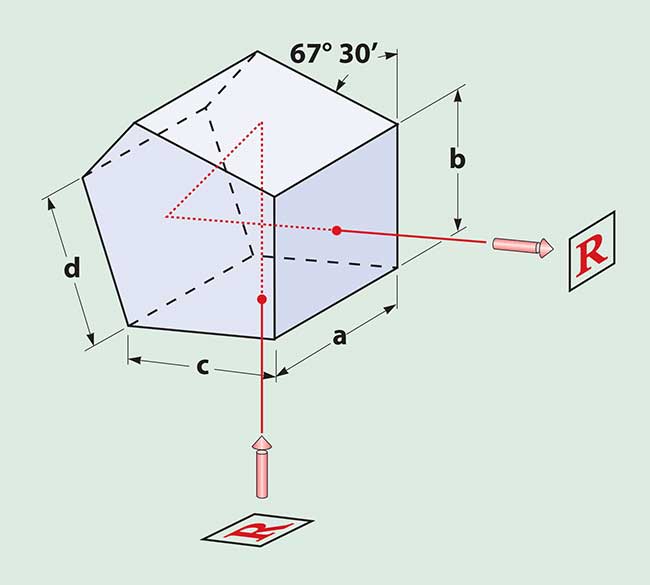
Figure 9. Penta prisms deviate a beam by 90° but do not reverse the image.
Reflective components
Mirrors are used to redirect, image and focus light and come in many sizes, shapes and configurations. They can be made from glass, metal or plastic; they can be flat (plane), spherical or pyramidal; and they can be coated or uncoated. The reflective properties depend on the wavelength, angle of incidence and polarization of the incident light. Fundamental mirror specifications include reflectivity at the appropriate wavelength, dimensions and tolerances, surface quality, clear aperture, and mechanical and thermal stability.
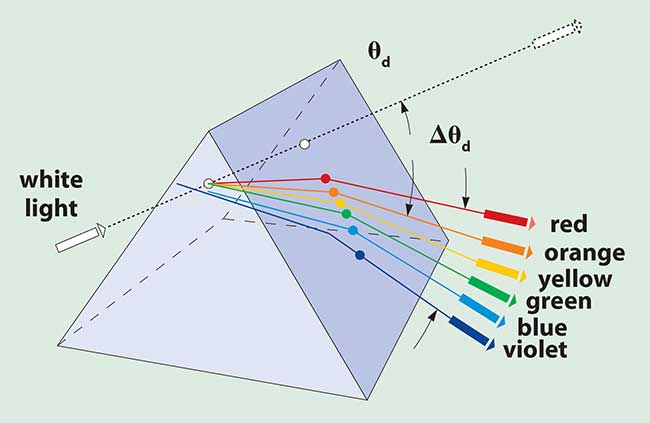
Figure 10. The equilateral dispersing prism separates wavelengths.
Metal mirrors are often uncoated, relying on a highly polished surface to reflect the light. Mirrors made with other substrates almost always include a metallic or dielectric coating (Figures 12, 13).
First-surface flat mirrors, sometimes called plane mirrors, are typically used to redirect light along an optical path or to fold optical systems. They transfer radiation with minimum effect on wavefront or image quality, and they can be combined to change the orientation of an image (similar to reflections through a prism).
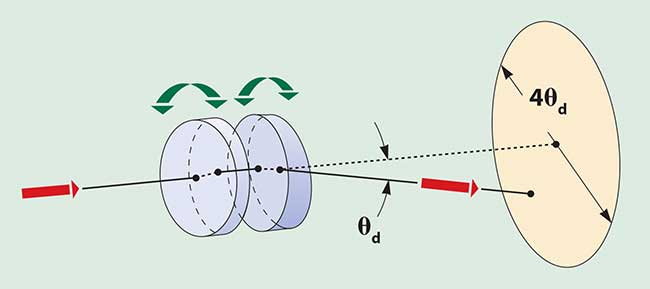
Figure 11. Wedge prisms are used in beam-steering applications.
The flatness of a plane mirror can be critical, particularly for applications involving images or large beam sizes because variations can alter the reflected wavefront and increase image distortion. Surface quality is important for laser applications because the light will scatter when large scratches and digs are present. Wedge or parallelism of the mirror substrate can be critical, particularly when replacing components in prealigned systems. Prisms with a reflective coating also function as excellent mirror alternatives.
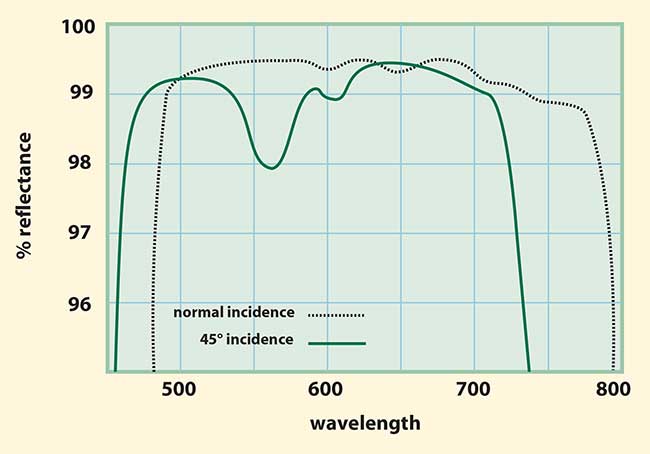
Figure 12. Broadband dielectric mirror coatings like the MAXBRIte /001 are deposited on glass substrates.
Spherical concave mirrors and reflectors are useful for focusing or collimating light and increasing the light output of illumination or projection systems. It is important to know the radius of curvature and its tolerance in order to align and position concave mirrors and reflectors correctly.
Retroreflectors reflect an incident beam back onto itself. They are used for aligning laser-based systems, making distance measurements, and in a variety of detection applications. Retroreflectors consist of three surfaces arranged to form a corner. Solid retroreflectors (also known as corner cubes) are made from a single piece of glass. The reflecting surfaces may or may not be coated, since TIR applies for most visible wavelengths. Hollow retroreflectors are constructed by assembling three flat mirrors into a mutually orthogonal inside corner.
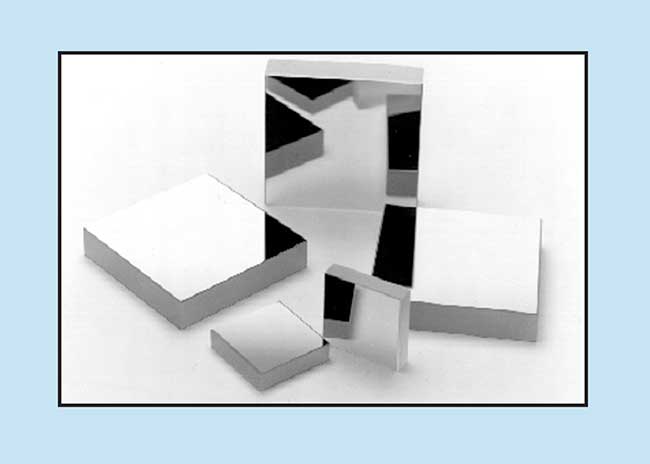
Figure 13. MAXBRIte (Multilayer All dielectric Xerophilous Broadband Reflecting Interface) coated square flat mirrors provide a minimum reflectance of 98 percent over a broad spectrum. Three coatings cover the range of visible to near-IR wavelengths.
Although solid retroreflectors are more stable than hollow ones because they stay in alignment despite environmental changes, hollow retroreflectors have several distinct advantages: Since the optical path is in air, they can be used from the UV to the far-IR; and, because the beam undergoes only front-surface reflection, dispersion effects are minimized and the polarization state of the light is affected far less than with solid retroreflectors.
A right-angle prism can function as a retroreflector in one dimension by having light enter and exit through the hypotenuse surface (Figure 14). An antireflection coating on the hypotenuse face improves a prism's retroreflector capability as long as the acceptance angle limitations for TIR on the roof faces are not exceeded.
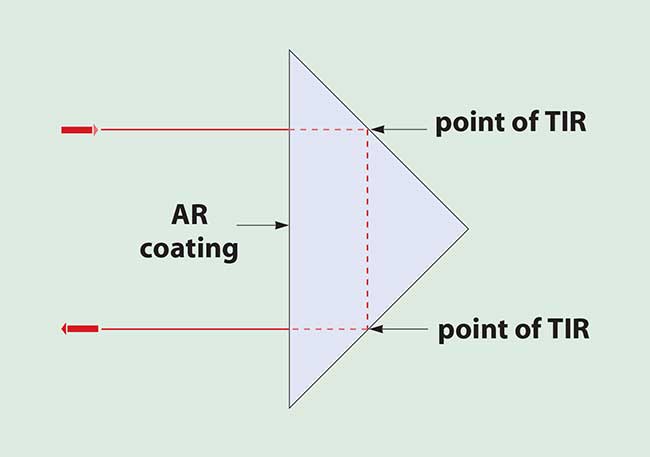
Figure 14. A right-angle prism can be made into a retroreflector by applying an AR coating to the hypotenuse face.
Diffuse reflectors
Diffuse reflectors scatter incident light evenly. The amount and distribution is a function of substrate surface quality, with rough surfaces scattering more light. Diffusers can reduce the intensity present in a beam by scattering it in several directions.
Absorbers are the inverse of reflectors because they prevent radiation from being reflected or transmitted. They are useful in applications where radiation must be removed from a system as in high-energy laser applications where stray reflections can damage other components. Absorbers are often limited by how much heat or laser power they can absorb before breaking down.
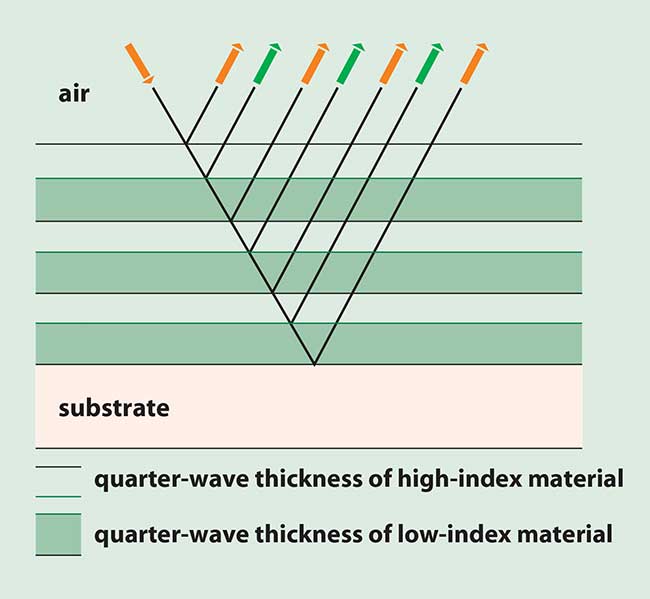
Figure 15. High-reflectance coatings are made from alternating layers of high- and low-index materials.
One other important consideration is that certain materials will absorb certain wavelengths better than others. This may be an advantage when blocking specific areas of the spectrum is required.
Diffraction gratings can separate polychromatic (white) light into specific wavelengths. Incident light is dispersed as a function of angle of incidence, wavelength and the spacing between the periods or parallel grooves. Gratings can be either ruled or holographic. Ruled gratings employ closely spaced parallel grooves on a substrate topped with a coating. Holographic gratings result from interference patterns made from a laser and a photolithography process. Diffraction gratings are most commonly used in monochromators and in spectroscopy applications. They are useful for scanning the spectrum for specific wavelengths or wavelength intervals.
Coatings
Thin-film coatings enhance performance and durability. They can increase the transmission of a lens or create the reflectance surface of a mirror and can be applied to substrates varying from typical crown glass to Zerodur, an ultralow-expansion, thermally stable glass. Coatings provide high or low reflectance at single or broadband wavelengths at a variety of incidence angles. Coatings can be optimized for wavelengths from 200 nm to the far-IR and are either metal or dielectric in composition.
Antireflection (AR) coatings are thin-film coatings that reduce the amount of light reflected from an optical element, thus increasing transmission. AR coatings are particularly important for systems with a large number of optical surfaces or a limited amount of light.
Whenever light is incident on the boundary between two media, air and glass for example, light is both reflected and transmitted. The amount reflected at normal incidence from a glass surface, assuming an index of 1.0 for air, can be calculated from Fresnel's simple equation:
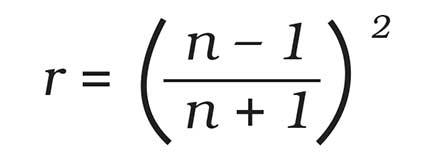
where n is the refractive index of the glass. For n = 1.52 (crown glass), the reflectance from the glass surface is 4 percent. This means that about 4 percent of all illumination incident normally on an air-glass surface will be reflected. In multielement lens systems without antireflection coatings, losses will be high. Magnesium fluoride (MgF2), the most common single-layer AR coating, is typically optimized for 550 nm at normal incidence. Special MgF2 coatings can be optimized for any wavelength from 200 nm to the near-IR and for almost any angle of incidence. This durable broadband coating reduces reflectance to less than 2 percent throughout the visible spectrum while accepting large-angle converging beams.
Broadband AR coatings are multilayer coatings that have a very low reflectance over a broad spectral range. Compared with single-layer MgF2 coatings over similar wavelength regions, broadband coatings typically reflect three to four times less light. They are slightly more sensitive to angle of incidence than single-layer coatings, but they can be optimized for specific wavelength ranges and angles of incidence.
V-coatings, which get their name from their v-shaped reflectance curve, are multilayer AR coatings that reduce a component's reflectance to near zero for one specific wavelength. Typically designed for normal incidence, they can achieve a maximum reflectance of less than 0.1 percent at their design wavelength. They can be optimized for almost any angle of incidence.
Reflection coatings enhance the performance of mirrors, beamsplitters, and bandpass or rejection filters. They may be applied to the outside surface of the component, creating a first-surface mirror, or to an internal surface, creating a second-surface mirror.
Metallic coatings are broadband and less sensitive to incidence angles than dielectric coatings. Common metallic coatings are aluminum, silver, gold and rhodium. Metallic coatings provide good performance and are economical. Many are supplied with protective overcoats that extend lifetime and retard oxidation. Protective coatings can reduce the amount of reflectance of a bare metal coating, but for most applications, the sacrifice in reflectance is negligible when measured against durability.
A popular and economical reflective coating is aluminum. Bare aluminum has high reflectance but oxidizes over time. Protected aluminum is preferred because its dielectric overcoat arrests the oxidation with only a slight sacrifice in performance. Most mirrors have this coating.
Enhanced aluminum, an improved version of protected aluminum, provides higher reflectance values in the mid-visible region. It is typically harder than protected aluminum and offers good abrasion resistance.
Bare silver is used almost exclusively in internal reflection applications such as prism faces; otherwise, it oxidizes and tarnishes. Silver offers better reflection in the near-IR than aluminum. Protected silver offers the same excellent performance as bare silver with the durability of a dielectric coating. Silver mirrors are ideal for low-power Ti:sapphire applications because of their low dispersion combined with high reflectance.
Gold provides consistently high reflectance from near- to far-IR. It is especially effective in controlling thermal radiation. On the other hand, bare gold is very soft and scratches easily. Protected gold combines the natural spectral performance of gold with enhanced durability.
High-reflectance dielectric coatings work in the same way as dielectric antireflection coatings. Quarter-wave thicknesses of alternating high- and low-refractive-index materials are applied to the substrate, forming a dielectric multilayer. By selecting appropriate combinations of materials, several reflective wavefronts are created. Constructive interference produces a highly efficient reflector (Figure 15). Multilayer dielectric coatings offer excellent performance at a specific wavelength or over a specified wavelength range. They are more sensitive to angle of incidence than metallic coatings, but they are harder and more resistant to abrasion.
High-reflectance coatings at specific wavelengths, designed for extremely high performance, are optimized for one angle of incidence. These coatings, commonly used in laser-positioning optics, are durable and can handle a modest amount of energy.
Broadband mirror coatings offer high reflectance over a spectral range typically greater than 200 nm. Typically optimized for a large angle of incidence, they can withstand high levels of illumination without damage.
High-energy coatings are targeted at applications involving concentrated laser beams where energy densities can reach kilowatts per square centimeter or higher. In addition to wavelength and reflectivity, a critical specification for a high-energy coating is damage threshold. For pulsed-laser applications, damage threshold is given in terms of energy per unit area over a specific time duration (e.g., 12.5 J/cm2 in 10 ns); for continuous wave (CW) applications, it is specified in terms of power per unit area (e.g., 1 kW/cm2). High-energy coatings are usually deposited in an automated, ion-assisted vapor-deposition chamber. As the thin film is deposited on the substrate, ion bombardment packs the molecules together, creating a dense, hard coating that can withstand high energy densities.
Low-dispersion coatings are designed specifically for use in ultrafast laser applications. When an ultrashort pulse (e.g., 50 fs) is reflected off a mirror, the pulse is broadened slightly. With a metallic coating like silver, the broadening is only a few percent, but with a standard dielectric coating, the pulse can be broadened 30 percent or more. Unfortunately, the metallic coatings often cannot withstand the high power densities associated with femtosecond lasers. Low-dispersion dielectric coatings can withstand the power and limit pulse broadening to 18 percent or less.
The family of optical components includes hundreds of individual types and configurations for an enormous number of applications; however, they all can be broken down into two simple classifications: transmissives and reflectives. Substrate materials and coatings enhance individual component performance. It is important to consider your particular application and requirements when designing an optical system, balancing cost, durability and image accuracy.
/Buyers_Guide/CVI_Melles_Griot/c3301