Modern coating technology offers the lighting system designer a number of ways to deal with heat radiation.
Eric Krisl, Deposition Sciences Inc.
Controlling and minimizing heat output is desirable in most lighting applications. For example, conventional incandescent light sources are very inefficient with only a small portion of the electrical power used converted into visible light. If the entire output from a tungsten bulb is concentrated in a projection system or a spotlight, a tremendous amount of unnecessary heat is also put through the system. This can make it uncomfortable and even unsafe for performers. It can also damage heat-sensitive materials such as plastic optical fiber or mirrors.
This article will explore ways in which optical coatings can achieve the desired separation of light from heat in lighting systems design.
The theoretical output radiance for a 3200 K color temperature source, such as a tungsten bulb, is shown as a function of wavelength (Figure 1). Wavelengths visible to the human eye, 400 to 700 nm, are highlighted in the graph. This clearly indicates that the peak emission from a source at this color temperature is far outside the visible spectrum and the bulk of the energy from such a source is at wavelengths not visible to the human eye. Most of the output occurs in the infrared (IR) spectral region. The human body senses infrared radiation as heat.
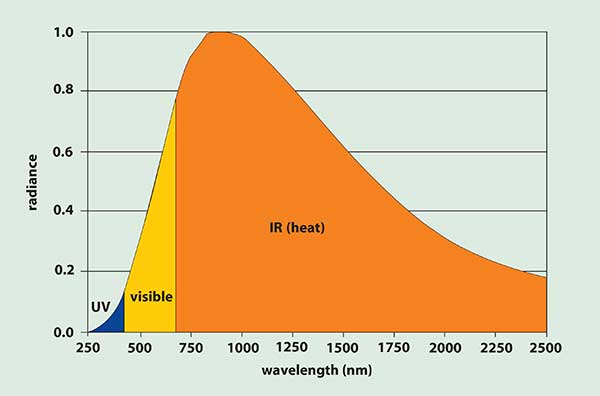
Figure 1. Typical radiance for a 3200 K tungsten source.
What to do?
Ideally, we would like to be able to separate the infrared radiation from the visible light. There are two ways to accomplish this — optics that selectively reflect or transmit the unwanted infrared, or optics that selectively absorb the infrared.
Practical optical coatings consist of layers of varying thickness. This complexity allows them to reflect efficiently and selectively a range of wavelengths, as well as function at a range of incidence angles. Multilayer coatings can be designed to alter the reflecting characteristics of the substrate to produce antireflection, high reflection, spectrally selective and polarization-sensitive effects over both a broad wavelength range and a large range of incidence angles. The coatings discussed here are spectrally selective coatings, which separate the visible and infrared wavelengths.
Optical coatings are conceptually simple to understand and, thanks to modern software, easy to design. However, manufacturing them is as much art as science. To achieve the desired result, it is necessary to control precisely the layer thickness and material indices of refraction. Given that layer thicknesses are typically less than a quarter of a micrometer and that minute changes in material microstructure can influence refractive index, this is not easy to accomplish, especially on a production basis. The ability of the coating itself to withstand the high heat loads without failure is critically important for an effective heat control application. Good adhesion and layer integrity are also important if the optical coating is to be environmentally durable.
Several options
There are several methodologies for producing thin-film optical coatings, with each technique having its own variations. Sputtering and low-pressure chemical vapor deposition (LPCVD) have both been successfully employed to make heat control coatings.
Sputtering is typically performed in a cylindrical chamber, where the sputtering targets (i.e. the coating materials) are arranged around the periphery. The optical parts or surfaces to be coated are held on a rotating drum concentric with the chamber.
In action, the chamber is first evacuated and then filled with a low-pressure inert gas such as argon. A voltage is applied to the coating material target(s), (usually a metal or semiconductor), which ionizes the gas in the region around the target, forming a plasma. Ions from the plasma are accelerated into the target, causing atoms to sputter off the target material. These atoms then fill the chamber, and some are deposited on the surface of the optics. Due to the presence of the low-pressure gas, the movement of the sputtered atoms is partially randomized, causing uniform coating, even over highly curved surfaces or parts with unusual geometries.
If a small amount of oxygen is introduced into the machine during this process, sputtered material atoms will react with it on the substrates, forming oxides. The process, called reactive sputtering, allows for the production of multilayer oxide coatings that feature excellent mechanical and thermal characteristics.
In all sputtering techniques, the sputtered target atoms come out with a large amount of energy, leading to inherently hard coatings. By hard coatings, we mean coatings that have greater mechanical and thermal stability.
At Deposition Sciences Inc. we have developed an effective approach to reactive sputtering, called MicroDyn, where the sputtering is augmented by microwave plasma that forms a wider range of oxygen species (ozone, etc.) to enhance the reaction process.
Chemical reaction
In LPCVD, the coating material is created through a chemical reaction, rather than being sputtered from a target of the material itself. Specifically, in LPCVD, the parts to be coated are put into an evacuated chamber called the reactor, and heated to a temperature sufficient to drive a surface chemical reaction. This temperature is typically above 400 °C. The reactor is filled with a chemical vapor, and all exposed parts of the substrate are uniformly coated. This makes LPCVD particularly useful for coating parts with unusual shapes, such as lamp envelopes or shaped reflectors. LPCVD coatings are in general, hard and durable with good heat-handling characteristics.
Depending upon the type of components being used and the allowable geometry of the setup, there are a number of possible approaches to the deployment of heat control coatings. In all cases, however, the goal is the same: to separate the useable visible wavelengths from the longer, damaging infrared heat wavelengths.
One way of accomplishing this goal is to introduce a component into the light path which reflects visible wavelengths and transmits infrared wavelengths. Such an element is called a cold mirror. With a cold mirror in place, the visible light is redirected into the desired path, and the heat energy is passed through, where it either continues out of the system, or is absorbed at some point (Figure 2, top).
Figure 2. Three types of heat control coatings.
Given this functionality, cold mirrors must be fabricated from substrates that transmit infrared radiation. Commonly used materials are glass, Pyrex and fused silica; the latter because of their high heat-handling capability. These can be ground and polished (or even molded) into a variety of shapes, including flat mirrors or curved reflectors that collect and redirect the bulk of the light from a source.
The actual cold-mirror coating is a complex multilayer film, typically 20 to 40 layers. Some cold-mirror coatings use sputtering or LPCVD to deposit several materials into a film that provides high temperature handling capabilities, meaning long life-time in actual use.
Components that do the opposite of a cold mirror, namely reflect the infrared and pass the visible, are called hot mirrors (Figure 2, bottom). These are also complex, multilayer films (50 to 100 layers), usually produced using reactive sputtering or LPCVD technology and typically deposited on high temperature-handling, transmissive substrates. Their fabrication and use is essentially the same as for cold mirrors, other than requiring different system geometry to take into account their reversed functionality. As a result, hot mirrors are generally produced on flat substrates, and are not typically applied to curved reflectors.
Envelope coating
One specialty application of hot mirror technology that we developed is referred to as envelope coating. In this case, a hot-mirror coating is deposited directly on the glass envelope of the bulb itself. With a hot-mirror coating applied to a roughly spherical bulb with a well-centered filament, a portion of the infrared output is directed back onto the filament, and never escapes the bulb. The infrared light, which is focused back onto the filament, acts as another energy source for heating it up. The result is that less electricity is required to bring the bulb up to a given color temperature output. This envelope coating approach provides the dual benefit of eliminating heat right from the beginning of the system, as well as yielding a more energy-efficient source. Given the increasing need for energy conservation, demands for this energy-efficient incandescent light source are also increasing.
Producing bulbs with these coatings requires close cooperation with the lamp manufacturer. Bulb envelope shape, filament size, placement and shape, and coating design must all be optimized to work together. Unfortunately, it is typically not possible to coat existing bulbs for end users.
Many high-intensity stage lighting systems use spun aluminum metal reflectors, as opposed to glass reflectors. These offer superior mechanical durability to glass, and are easier and cheaper to fabricate in large sizes. Normally, aluminum has higher reflectivity in the infrared than in the visible, so that heat is efficiently collected and passed through the optical system, the exact opposite of the desired effect.
Since the substrate material (aluminum) is not transmissive to infrared radiation, the standard cold-mirror coatings described earlier are not useful in this situation by themselves. Instead, it is desirable to coat these reflectors with a coating that enhances absorption of the infrared radiation, so it is not passed through the optical system. While this does cause heating of the reflector itself, this can be dissipated through subsequent conductive (heat sink) or convective (fan) cooling.
Coatings that absorb infrared in the manner just described are one example of selective absorbers known as dark mirrors (Figure 2, middle). Due to the large amount of heat they must tolerate, it is imperative that dark mirrors have excellent thermal durability.
To further enhance the reflectivity of the aluminum reflector in the visible, a cold mirror is also usually applied on top of the dark mirror. This type of coating can also be used to adjust the color characteristics of the reflected light, and is thus useful as a means of altering color temperature.
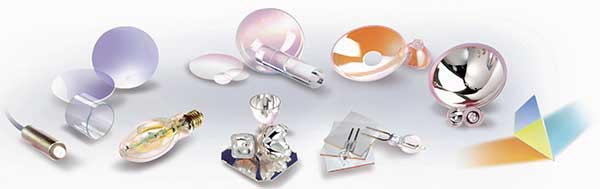
Figure 3. Coating solutions for various commercial lighting applications.
Advanced optical coating techniques offer lighting system designers a variety of means to manage heat radiation, as well as to produce filters and other optics for color control or specialized visual effects (Figure 3). Given the numerous options in achieving these results, it is imperative that a system designer works with a coating provider who understands the industry and who can provide the ideal manufacturing method required for an optimum, cost-effective solution.