Using the proper adhesive in the assembly of fiber optic components not only saves time and expense, but also can improve reliability and performance.
Edward A.Y. Fisher, Henkel Corp.
Adhesives for fiber optic components that perform well on glass, metal, ceramic and most plastic substrates provide excellent chemical and solvent resistance. They also can act as an electrical insulator and may be used in high-strength optical alignment applications. In addition, they can bond dissimilar materials quickly and efficiently, enabling the production of many optical components that would be impossible to make using mechanical fastening methods.
Adhesive technology has always played a role in fiber optics assembly. Initially, epoxy technology was the method of choice, primarily in the connector market, but today’s adhesives are highly engineered products available in a wide variety of choices to help fabricate fiber optic assemblies.
Adhesives’ benefits
By choosing the correct adhesive, manufacturers can speed fabrication, lower costs and improve reliability and performance. Adhesives allow stronger, faster devices to be made more cost-effectively, meeting the demands of the marketplace.
Adhesives offer several major benefits over other methods, such as nuts and bolts, rivets, welding and soldering, any of which can create localized stress points. Welding and soldering can introduce unwanted heat to the device and are not effective on dissimilar substrates. They also require highly skilled assemblers.
On the other hand, adhesives distribute stress load evenly over a broad area, reducing strain on the joint. Because they are applied inside the joint, they are invisible within the assembly. They resist flex and vibration stresses, and form a seal as well as a bond, protecting the internal components from harsh environments. They join irregularly shaped surfaces more easily than mechanical or thermal fastening, add little weight, create virtually no change in part dimensions or geometry, and quickly and easily bond dissimilar substrates and heat-sensitive materials. Adhesives are “one size fits all,” and assembly can be automated easily.
One limitation is the curing time, which is the amount of time it takes for the adhesive to reach its maximum strength and fixture. Other drawbacks include surface preparation requirements and the potential need for future joint disassembly.
Design considerations
When selecting adhesives, manufacturers should consider the three aspects of a bonded assembly — the parts that make up the component, the assembly process and the adhesive — and how they will affect device production (Figure 1).
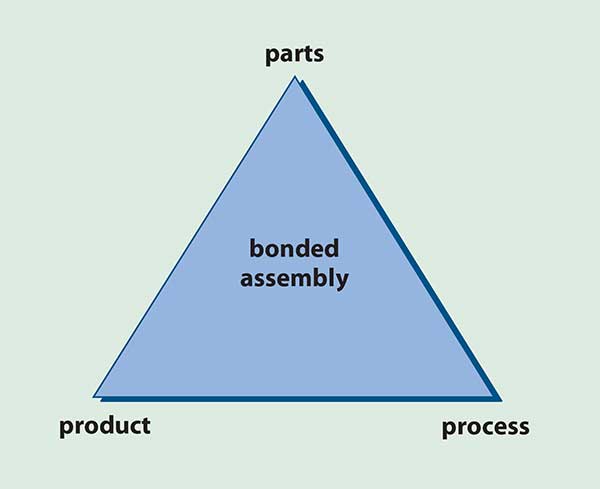
Figure 1. The three variables that will affect device production include the component, the assembly process and the adhesive.
To select an appropriate adhesive, a designer should consider how the device will be assembled and what substrates will be bonded. It also is critical that the adhesive specified during the design phase is appropriate for the production process.
Three properties are key to the application of an adhesive: glass transition temperature, outgassing and testing that involves placing samples in an environmental chamber set at 85 percent relative humidity and 85 °C.
Outgassing is the evolution of unreacted or unbound product when the adhesive is subjected to high heat. These properties are called out in Telcordia specification GR-1221.
Glass transition temperature is the temperature at which an adhesive transforms from hard and glassy to soft and rubbery. It can be measured using dynamic mechanical analysis, thermal mechanical analysis or differential scanning calorimetry. All three techniques are accepted in the industry and provide different results based on spectral interpretation.
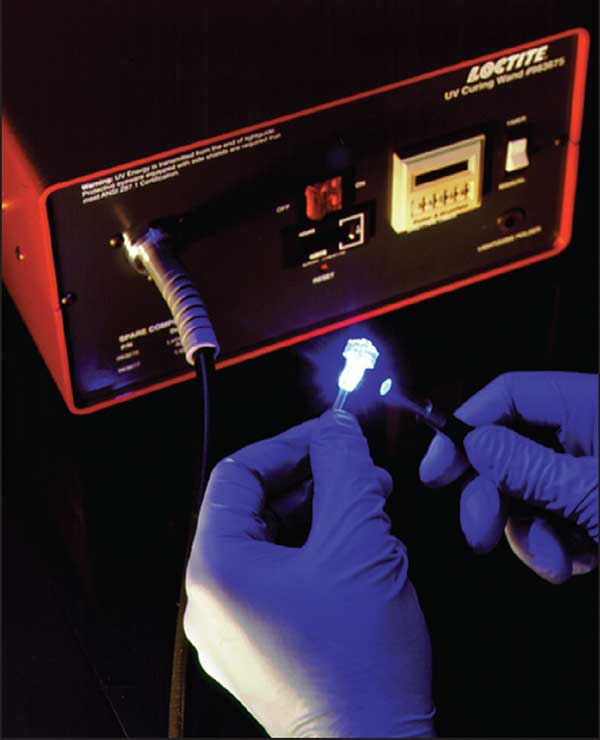
Figure 2. A light-cure adhesive, previously applied to a clear plastic part, is undergoing manual spot curing.
Dynamic mechanical analysis is generally accepted as having excellent repeatability with good dependability. Regardless of technique, the Telcordia specification calls for a minimum glass transition temperature of 95 °C. A high transition temperature does not guarantee a “pass” in heat/humidity aging. Cyanoacrylate adhesives can have temperatures much higher than 95 °C, yet they will fail in a hot, moist environment. For cyanoacrylates, a high temperature does not equal high performance. There are low-temperature (60 °C) UV acrylics that have outstanding adhesion to glass and that will not lose adhesion after 2000-plus hours of damp heat testing.
Without industry guidance, most engineers gravitate toward the NASA outgassing specification for total mass loss and collected volatile condensable materials. However, it is up to the end user to determine the acceptable outgassing levels for an adhesive. A low-outgassing adhesive tested at 85 °C for a few hours seems more realistic than the NASA test of 24 hours at 120 °C in a vacuum. Those with hermetically sealed packaging may have to use low-outgassing products that meet the NASA specification to avoid adhesive condensation on sensitive optics.
The aggressive 85 percent humidity, 85 °C test, or 85%RH/85C, is the final and most important criterion for obtaining Telcordia certification. The high test temperature will cause materials with a glass transition temperature at or below 85 °C to become soft and rubbery, allowing moisture to penetrate the adhesive bond line and causing the assembly to delaminate at the adhesive/substrate interface. This test, considered one of the toughest in the industry, is used in the fiber optics market and other communications markets as the benchmark for determining the life of a device.
Other adhesive performance criteria that may affect an assembly are product shrinkage upon cure, optical clarity and transmission (if the adhesive is in the light path), viscosity (for processing), thermal expansion and hardness.
If properly selected, adhesives can deliver easily assembled, high-performance fiber optic devices that will provide years of predictable service and reliability.
Available technologies
Of the many adhesives available, five families are most commonly used in fiber optics assembly. Each offers a combination of performance and processing benefits.
Epoxies: Long the workhorse of the fiber optics industry, epoxies are common one- or two-part structural adhesives that bond well to a wide variety of substrates, have low outgassing levels and shrink minimally upon cure. Their major disadvantage is that they tend to cure much more slowly than other adhesives, with typical fixture times from 15 minutes to two hours. Two-part epoxies also must be thoroughly mixed to ensure best performance.
TABLE 1.
TYPICAL PROPERTIES OF ADHESIVES
|
|
|
Epoxies
|
|
UV Acrylics |
|
Silicones |
|
Cyanoacrylates |
|
Anaerobics |
|
|
|
|
|
|
|
|
|
|
|
|
|
Refractive Index
|
|
1.56 |
|
1.51 |
|
N/A |
|
N/A* |
|
N/A* |
|
|
|
|
|
|
|
|
|
|
|
|
|
Glass Transition
Temperature (°C) |
|
50 - 150+ |
|
50 - 100+ |
|
<—40 |
|
100 - 130 |
|
100 - 130 |
|
|
|
|
|
|
|
|
|
|
|
|
|
Coefficient of Thermal
Expansion (ppm,
Below Glass Transition
Temperature)
|
|
250 - 400 |
|
90 - 120 |
|
250 - 400 |
|
90 - 120 |
|
90 - 120 |
|
|
|
|
|
|
|
|
|
|
|
|
|
Outgassing |
|
2 - 5/
0.1 - 0.7 |
|
1 - 4/
0.06 - 0.25 |
|
1.5 - 2.0/
0.7 - 1.5 |
|
5 - 6/
0 - 0.001 |
|
Strength -
dependent |
|
|
|
|
|
|
|
|
|
|
|
|
|
Shrinkage (%) |
|
1.5 or less |
|
2.25 or less |
|
0 - 3 |
|
5 - 15 |
|
5 - 13 |
* Not typically used in the bond line
Despite their cure time, epoxies are a favorite in fiber optics assembly because of their high glass transition temperature and low shrinkage properties. Available in small package sizes, easy-to-mix two-part “bipack” epoxies are extremely popular because they minimize adhesive waste and accommodate small production runs. One-part, premixed heat-cure epoxies also are popular, although work life becomes short once the adhesive is removed from cold storage. Dual-cure (UV and/or heat) epoxies are a recently introduced option that increases processing speeds. As production volumes increase, assemblers can use larger volume, side-by-side static mix products.
Two-part epoxies are used extensively in bonding fiber to ferrule. They also are used for potting electronic components, bonding dissimilar materials such as ceramic or glass to aluminum. Epoxies also can bond secure strain relief boots and can secure fiber onto packages.
UV-curable acrylics: One-part, solvent-free, UV-curable acrylics offer performance benefits comparable to those of epoxies. These adhesives contain a photo-initiator that starts to cure when exposed to UV light. Although early UV-curable acrylic adhesives had low glass transition temperature, high outgassing and high shrinkage values that made them unsuitable for use in critical fiber optic devices, today’s UV technology provides glass transition temperatures greater than 100 °C, shrinkage of less than 1 percent and very low outgassing values. Because cured acrylic adhesives are thermoset plastics, they offer superior thermal, chemical and environmental resistance.
Traditional UV adhesives must be in direct UV light to cure — any adhesive in dark or shadowed areas remains uncured. However, new light-cure acrylic formulations are available with a secondary cure mechanism (such as exposure to heat or chemical activators) that allows the adhesive to cure completely in shadowed areas. Because cure is on demand, light-cure acrylics offer extended open times for positioning and repositioning parts. These adhesives have high bond strength with a wide variety of substrates and come in varying degrees of flexibility, from soft elastomers to glassy plastics. All this, coupled with cure times of just two to 60 seconds, makes UV-curable acrylics an attractive alternative to epoxy technology.
The clarity of UV acrylics enables their use in the light path for bonding glass ferrules and for attaching direct fiber. They also are used in V-groove and lens bonding, critical laser alignment, potting fiber bundles and leads, coating ribbon cables and block bonding/sealing.
Silicone: For bonding dissimilar substrates such as glass to metal, the best option to ensure a robust assembly is silicone technology. Silicones are flexible, rubberlike materials that cure at room temperature, exhibit excellent resistance to heat and moisture, and bond a wide variety of substrates. Their pliability over a broad temperature range (–40 to 250 °C) makes them ideal stress absorbers. Today UV-cure, UV/moisture-cure, heat-cure and two-part silicone technologies complement the older moisture-cure chemistry. Moisture-cure silicones require a minimum amount of ambient moisture to ensure maximum performance.
Silicones are used to bond ceramic and epoxy glass boards to metal packages, to toughen tall components, gasket and seal packages, and to pot components exposed to extreme temperature swings.
Cyanoacrylates: High-strength, one-part cyanoacrylates are commonly used as processing aids in fiber optics assembly. They are instant adhesives, also known as “super glue.” Although their structural bonding properties are inadequate for most fiber optic assemblies (because they do not adhere well to glass and have poor high-temperature resistance), they excel at temporarily tacking down fiber, components and boards while the permanent adhesive is curing. They achieve fixture strength in just seconds and full strength within 24 hours. Cyanoacrylates are also used for locking screws, making setscrews tamperproof and bonding boots to ferrules.
Anaerobics: Traditional anaerobic adhesives, which are also known as threadlockers, are single-component substances that remain liquid when they are exposed to air. Once confined between metal substrates in the absence of oxygen, anaerobic adhesives cure or harden into tough thermoset plastics that provide excellent environmental and temperature resistance. These adhesives are ideal candidates for bonding fibers to ferrules because of their fast fixture time (minutes) and high ultimate strength. Anaerobics also are used in the traditional way to “lock” down lids in devices and to make setscrews tamperproof, ensuring that factory settings can’t be changed and helping to void any warranty claims for products that have been opened by the user.
Questions to Ask When Choosing an Adhesive
• Does the design include difficult-to-bond substrates such as gold plate, polypropylene or nylon?
• Are there dissimilar metals that may cause thermal expansion problems when heated?
• Are any of the parts UV-absorbing, making a UV-curable adhesive inappropriate?
• Are there shadowed areas that will not be directly exposed to UV light?
• Will surface treatments (plasma, corona treatment) enhance bonding?
• Will the substrates and adhesive perform properly in the end-use environment?
• Are there temperature-sensitive substrates that can’t tolerate heat, making the selection of a heat-cure or even a UV-cure adhesive inappropriate?
• What kind of joint stress will the assembly see? Tensile? Compressive? Peel?